
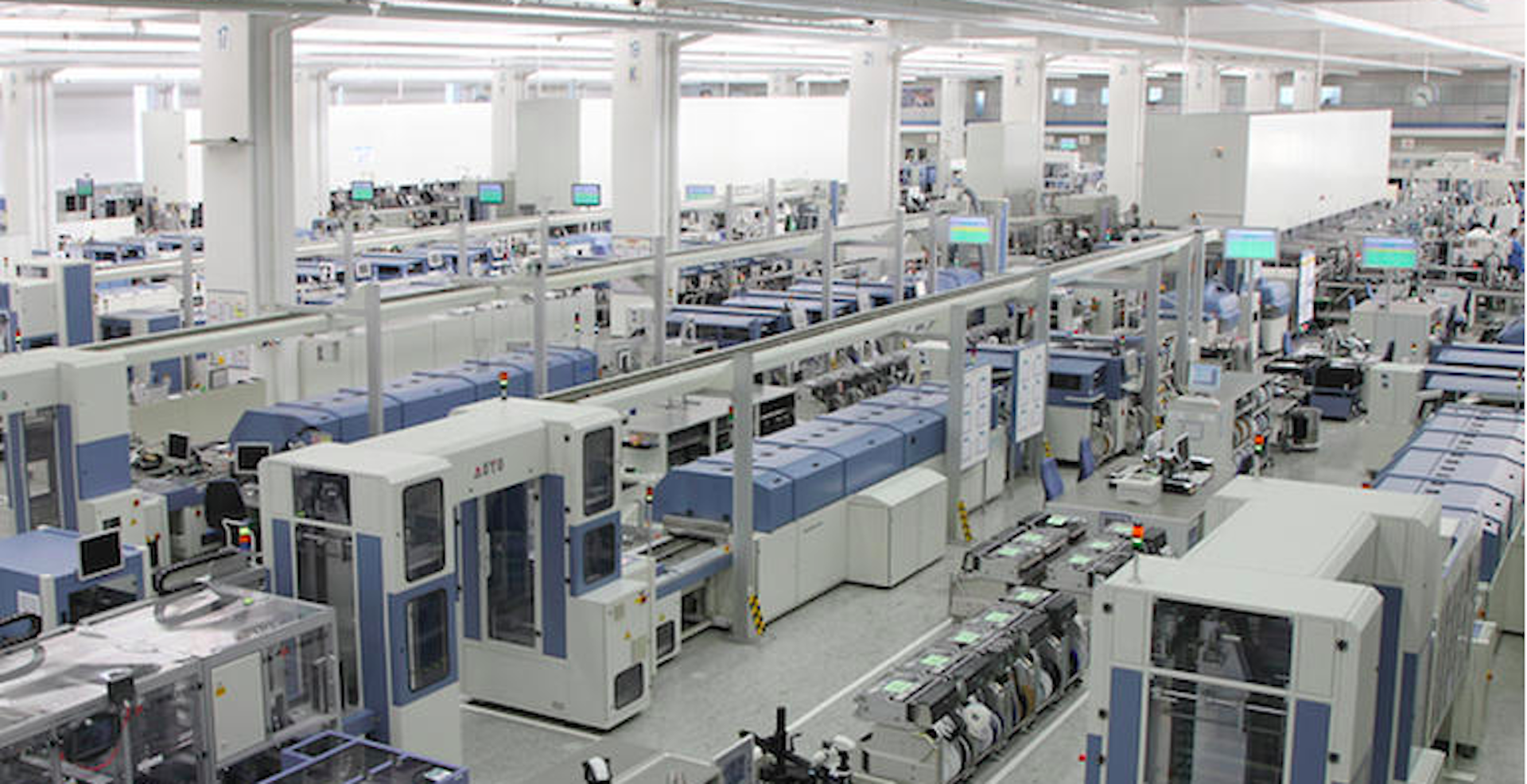
Here are some things any manufacturer assessing automation should consider. The goal should be to empower workers, to change the way they work rather than changing the fact of work. Rather, manufacturers will do better by automating the parts of manufacturing work that contribute to human error. Past attempts at lights out factories have shown us that it’s a mistake to engineer humans out of the factory. In other words, manufacturers should focus on “lights out processes, not lights out factories.” Things to Consider Before Turning the Lights Off We need to help humans do what they do best, and let automation rule on repetitive, tedious tasks. This observation is key to getting automation right. As much as 70% of human errors are really attributed to “organizational weaknesses.” In other words, humans make mistakes because complex or badly designed workflows set them up to fail. In a summary of years of research into human performance, system design, and workplace errors, the United States Department of Energy came to a surprising conclusion. We all know the cliche “to err is human.” What the pessimistic perspective on human performance gets wrong is that most human error isn’t attributable to mistakes. This haven’t proven to be the case, and here’s why. The problem is that the move to eliminate human labor entirely is based on a faulty assumption: if automation is more efficient and less error-prone than humans, then more automation will lead to greater efficiency.
#Lights out manufacturing manual#
As one analyst recently put it, “let’s face it: for some companies removing paper or eliminating a manual process would be a revelation.” The problem with lights out factories was never with the idea that some work should be automated. The key to getting automation right? Evolve how we work. Previous attempts at turning the lights off have all found that human flexibility is the best match for manufacturing’s complexity. Even manufacturing luminaries like AppleĪAPL have found that it’s hard to match human flexibility and precision. The engineering required to build fully automated lines is staggering and, if they break, diagnosing and solving the problem is an equally difficult task. Modern manufacturing lines can require decision making and sensitivity that’s hard to replicate with algorithms and robots.
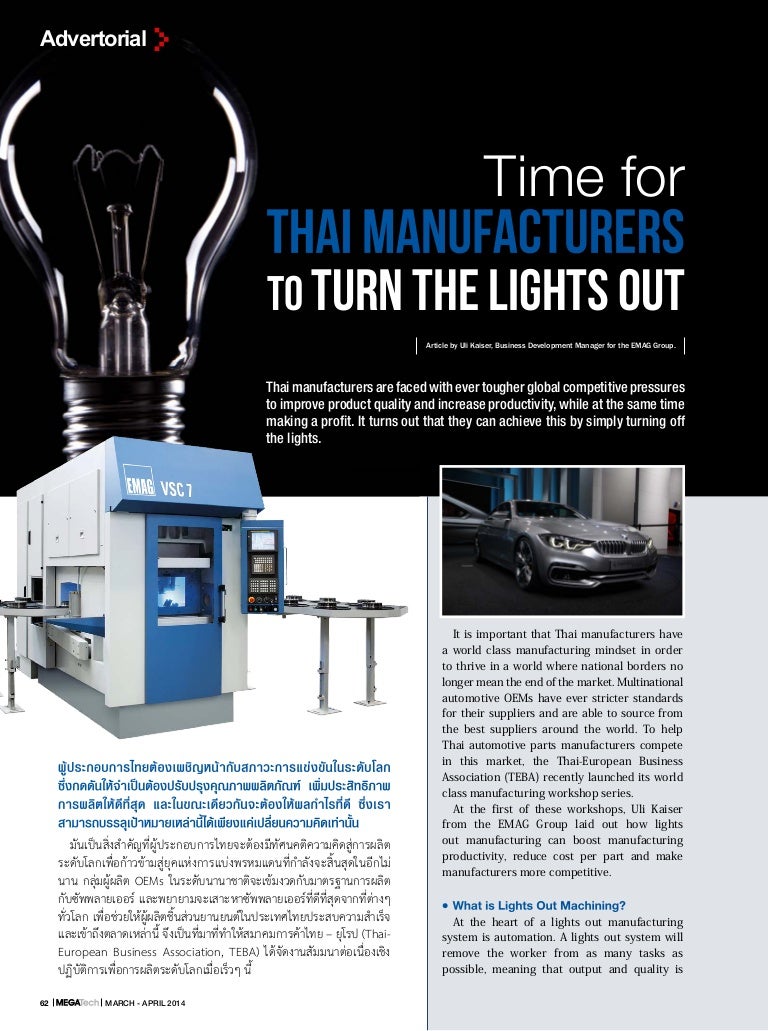
In reality, manual assembly requires an enormous amount of individual skill. There’s a misperception that manufacturing work is dull and repetitive. 1.) manufacturing work is complex, and 2.) automation is inflexible.
